La fiabilité en maintenance
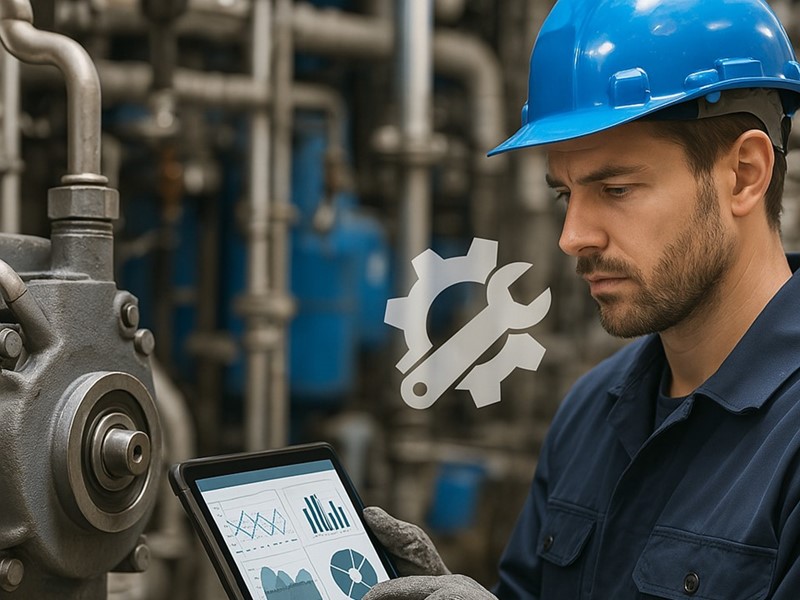
Un duo indispensable pour la performance industrielle
Dans le monde de l'industrie moderne, où chaque minute d'arrêt peut coûter des sommes considérables, la fiabilité et la maintenance ne sont plus de simples concepts, mais des piliers fondamentaux de la performance opérationnelle. Loin d'être des entités distinctes, elles sont intrinsèquement liées et complémentaires, œuvrant de concert pour assurer la disponibilité, l'efficacité et la pérennité des équipements.
La fiabilité : la promesse d'un fonctionnement sans accroc
La fiabilité est la capacité d'un équipement, d'un système ou d'un composant à fonctionner sans défaillance pendant une période donnée, dans des conditions d'utilisation spécifiées. C'est, en quelque sorte, la "promesse" que votre machine fera ce pour quoi elle a été conçue, et ce, de manière constante. Une haute fiabilité se traduit par moins de pannes inopinées, des arrêts de production réduits et, in fine, une meilleure productivité.
Atteindre une fiabilité élevée n'est pas le fruit du hasard. Cela découle d'une conception rigoureuse, d'une fabrication de qualité, du choix de matériaux appropriés et, bien sûr, d'une stratégie de maintenance efficace.
La maintenance : l'art de préserver la fiabilité
La maintenance est l'ensemble des actions techniques, administratives et de management, effectuées pendant le cycle de vie d'un bien, destinées à le maintenir ou à le rétablir dans un état dans lequel il peut accomplir la fonction requise. Elle est le bras armé de la fiabilité, intervenant pour prévenir les défaillances, corriger les anomalies et prolonger la durée de vie des équipements.
Il existe différentes approches de maintenance, chacune avec ses spécificités :
- Maintenance corrective : Elle intervient après la défaillance. C'est la plus réactive et souvent la plus coûteuse en raison des arrêts imprévus et des dommages potentiels.
- Maintenance préventive systématique : Basée sur un calendrier ou un nombre d'heures de fonctionnement, elle vise à remplacer ou entretenir des composants à intervalles réguliers pour éviter les pannes.
- Maintenance préventive conditionnelle : Fondée sur la surveillance de l'état des équipements (vibrations, température, analyse d'huile, etc.), elle déclenche des interventions lorsque des seuils critiques sont atteints, permettant d'optimiser le moment de l'intervention.
- Maintenance prévisionnelle (predictive maintenance) : Grâce à l'analyse de données et à l'intelligence artificielle, elle anticipe les pannes bien avant qu'elles ne se produisent, permettant une planification optimale des interventions et une minimisation des temps d'arrêt.
- Maintenance proactive (pas normalisée) : Cette approche va au-delà de la simple prévention des pannes. Elle vise à identifier et à éliminer les causes profondes des défaillances, améliorant ainsi intrinsèquement la fiabilité des équipements sur le long terme.
L'interdépendance au service de la performance
La relation entre fiabilité et maintenance est symbiotique. Une bonne fiabilité réduit le besoin de maintenance corrective, mais une maintenance efficace est essentielle pour maintenir, voire améliorer, la fiabilité des équipements. Investir dans des pratiques de maintenance avancées, notamment préventive et prévisionnelle, permet de :
- Réduire les temps d'arrêt imprévus : En détectant et en corrigeant les problèmes avant qu'ils ne deviennent critiques.
- Optimiser les coûts : En évitant les réparations coûteuses dues à des pannes majeures et en prolongeant la durée de vie des actifs.
- Améliorer la sécurité : Des équipements fiables et bien entretenus sont moins susceptibles de présenter des risques pour le personnel.
- Augmenter la productivité et la qualité : Un fonctionnement continu et stable garantit une meilleure production.
Vers une stratégie intégrée
Aujourd'hui, les entreprises performantes ne voient plus la fiabilité et la maintenance comme des départements séparés, mais comme des composantes intégrées d'une stratégie globale de gestion des actifs. L'adoption de logiciels de GMAO (Gestion de la Maintenance Assistée par Ordinateur), de capteurs IoT et de l'analyse de données permet de collecter des informations précieuses pour affiner les stratégies de maintenance et améliorer continuellement la fiabilité des équipements.
Méthodes de maintenance basées sur la fiabilité et sur les risques : un enjeu stratégique pour l'industrie
Dans un paysage industriel en constante évolution, la maintenance des équipements représente bien plus qu'une simple tâche opérationnelle ; elle est un levier stratégique et économique essentiel pour optimiser la productivité et assurer la pérennité des actifs.
Au cœur de cette problématique se trouvent les méthodes de maintenance basées sur la fiabilité (MBF, ou RCM pour Reliability-Centered Maintenance) et sur les risques. Ces approches, loin d'être statiques, ont connu des évolutions significatives, donnant naissance à un éventail de méthodologies adaptées aux défis spécifiques de chaque secteur.
Des origines aéronautiques aux applications industrielles diversifiées.
Le concept de la maintenance basée sur la fiabilité a vu le jour dans les années 1960 au sein de l'industrie aéronautique, sous l'impulsion des travaux pionniers de Nowlan et Heap en 1978.
L'objectif était clair : optimiser les programmes de maintenance pour garantir la sécurité et la disponibilité des aéronefs. La méthode MSG-3, toujours d'actualité dans l'aéronautique, a posé les bases de cette approche en se concentrant sur les fonctions de l'équipement, les modes de défaillance et leurs conséquences.
Fort de son succès, le concept a rapidement transcendé les frontières de l'aéronautique. Dès 1983, John Moubray a développé la méthode RCM2, une adaptation des principes de la MSG-3 à l'ensemble des secteurs industriels. Reconnue pour sa rigueur, la RCM2 est compatible avec les normes internationales telles que la SAE JA1011 et JA1012 (développées en 2001 par la Society of Automotive Engineers), qui définissent les critères d'une analyse RCM valide.
Plus récemment, la norme CEI 60300, établie en 2009 par le Comité Électrotechnique International, a étendu ces principes aux équipements et structures des procédés industriels.
Choisir la bonne méthode : une décision stratégique
Le choix de la méthode la plus adaptée aux besoins spécifiques d'une entreprise est crucial. Il dépend de nombreux facteurs, tels que la nature des équipements, le niveau de risque acceptable, les ressources disponibles, et les objectifs de performance et de sécurité. Une analyse comparative des avantages et inconvénients de chacune de ces approches est donc indispensable.
Les méthodes de maintenance basées sur la fiabilité et sur les risques ne sont pas de simples outils ; elles sont le reflet d'une prise de conscience que la maintenance n'est plus une activité à subir, mais un investissement stratégique pour la performance et la durabilité de l'outil de production. Leur maîtrise est un atout majeur pour toute entreprise souhaitant optimiser ses opérations et minimiser les risques associés aux défaillances techniques.
Les méthodes basées sur la fiabilité et les risques
La fiabilité est au cœur de nouvelles méthodologies qui transforment la maintenance en levier stratégique. Issues du monde aéronautique, les approches MBF (Maintenance Basée sur la Fiabilité) et RBM (Maintenance Basée sur les Risques) s’appliquent aujourd’hui à tous les secteurs industriels.
La MBF repose sur l’analyse des fonctions critiques, des modes de défaillance et de leurs conséquences. Elle permet de concevoir des plans de maintenance précis et efficients.
À cela s’ajoutent les méthodes simplifiées comme le Streamlined RCM ou le PMO, qui visent à rendre l’approche accessible et évolutive.
De leur côté, les méthodes basées sur les risques évaluent la probabilité et la gravité des défaillances pour prioriser les actions. Elles sont particulièrement utiles dans les industries à haut risque (nucléaire, pétrochimie, chimie) et s’appuient sur des normes reconnues comme l’API 580 ou le projet RIMAP.
L’OMF : L’Optimisation de la Maintenance par la Fiabilité
L’OMF vient enrichir ces démarches en mettant l’accent sur l’amélioration continue des plans de maintenance existants. Plutôt que de partir d’une analyse théorique, elle s’appuie sur les données du terrain : retours d’expérience, indicateurs de performance, historiques d’intervention.
Elle repose sur trois axes principaux :
- L’analyse des défaillances réelles pour identifier les faiblesses systémiques.
- L’ajustement dynamique des plans de maintenance pour les rendre plus pertinents.
- L’utilisation de KPIs tels que la disponibilité, les coûts de maintenance, ou les taux de défaillance pour orienter les décisions.
Grâce à cette approche empirique et agile, l’OMF permet de réduire les coûts, d’augmenter la fiabilité et de renforcer la résilience des installations.
L’Optimisation de la Maintenance par la Fiabilité (OMF) est une méthode stratégique qui vise à améliorer la performance des équipements industriels en s’appuyant sur leur fiabilité. Elle a été développée initialement par EDF et est aujourd’hui utilisée dans divers secteurs industriels
Conclusion
La Maintenance, Pilier de la Résilience Industrielle !
La fiabilité et la maintenance ne sont plus des fonctions périphériques : elles sont devenues les leviers de la performance industrielle. En combinant expertise technique, outils numériques, et méthodologies avancées, les entreprises peuvent construire une stratégie robuste, anticipative et durable. Investir dans cette vision intégrée, c’est s’assurer un avenir industriel résilient et compétitif.
Source
Article d'Antoine DESPULOLS "Optimisation de la maintenance par la fiabilité (OMF)" - Techniques de l'ingénieur.
Article de Gilles ZWIGELSTEIN "Méthodes de maintenance basées sur la fiabilité et sur les risques" - Techniques de l'ingénieur.
Antoine DESPUJOLS
Président de la Commission de normalisation « Maintenance » de l’AFNOR – Ingénieur consultant en maintenance – Administrateur AFIM, Association française des ingénieurs et responsables de maintenance
Gilles ZWINGELSTEIN
Ingénieur de l’école nationale supérieure d’électrotechnique, d’électronique, d’informatique et d’hydraulique et des télécommunications de Toulouse (ENSEEIHT), Docteur-Ingénieur, Docteur ès Sciences. - Professeur associé des universités en retraite, Université Paris Est Créteil, France
Réseau Maintenance
ACTUALITÉS
Nous Rejoindre
Au service de la maintenance depuis 1933…
Accédez au bulletin d'adhésion ou de renouvellement.
Nous Contacter
10, Rue Louis Vicat
75015 PARIS
01 56 56 29 29
Nous Contacter
Ouverture : sur rendez-vous
Contact internet ou téléphone.